FTI – Forming Suite Overview
FTI-Forming Suite is a Powerful, Simple To Use, Accurate Sheet Metal Material Cost Optimization Software.
Automotive OEM’S need to Optimize & Reduce Cost of Existing and New Vehicle Platform. Optimize Product Design to Improve Yield. Optimize and Set Vendor Target Cost.
Automotive Suppliers need to respond to RFQ quickly and accurately. Need to quote accurately wins business and maintain profit.
Forming Suite Product range for Sheet Metal Stamping Material Cost Estimation & Optimization Supports both Automotive OEM’S and Suppliers common Goal of “ Material & Process Cost Reduction”.
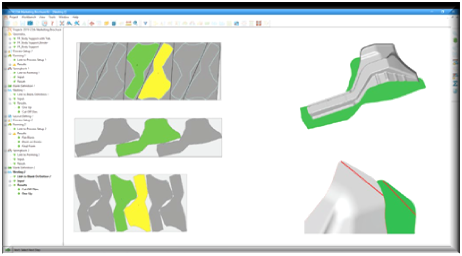
COSTOPTIMIZER®
FTI® CostOptimizer Is Used By Stamping Cost Engineers in Automotive OEM’S & Suppliers Costing Departments for quickly estimating the Material Cost Related to Sheet Metal Stamping Parts by Calculating the Blank Size of the component , Putting the blank in the strip layout in most optimum way so that the strip conforms to minimum scrap condition.
Saving or Reducing Scrap from any stamping process results in direct Cost Saving for the company.
Cost Optimizer Comprises of FTI Software’s unique and time tested solutions like , Fast Blank , Blank Nest , Strip Nest , Progressive Nesting & Product Design Optimizer.
Generates Reports with – Blank Size , Material Yield or Utilizations, Calculates Gross Wait for Sheet Metal Components.
Benefits – Price Panel , Vendor Development , Cost Control Management , Component Costing Departments.
COSTOPTIMIZER® Advanced
COSTOPTIMIZER® Advanced as a solution is to carry forward all the feature benefits of CostOptimizer® for Cost Control or Optimization by optimizing material yield through accurate Nesting’s. In order to further optimizer Stamping Cost , costing engineers need to optimize the process also.
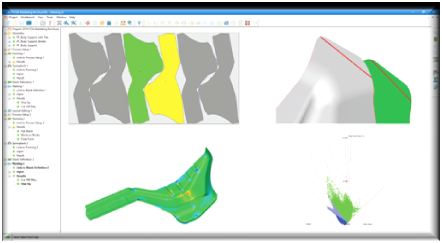
COA as a solution helps Product Designers to run and understand early feasibility and avoid costly ECN which may arise due to faulty product Design. Helps Cost Engineers to understand and define the stamping processes required to manufacture the component and establish process related cost.
COA – Outputs Thinning & Thickness Strain Plots, FLD, Wrinkle Formation Zones , Splitting Zones + Cost Optimizer Features.
Benefits – Product Design, Price Panel , Vendor Development , Cost Control Management , Component Costing Departments.
FormingSuite® PROCESSPLANNER
FTI Solutions usage not only standardises the Material Costing Process , but can also standardise the Costing Process of Stamping Dies.
FormingSuite® PROCESSPLANNER supports Process Planning & Die Cost Estimation as per Line Die Plan & Progressive Die Plan.
Forming Suite® PROCESSPLANNER combines the features of Formability Analysis , Blank Development & Blank Nesting Tools to calculate and generate Stamping Process Plans with documented reports which include the process sequence & No. of operations , press requirements , tool sizes and detailed costing for Transfer , Tandem & Progressive Dies.
COP – Outputs Process Plan , No. Of Stations , Detailed Die Costing report.
Benefits – Price Panel , Vendor Development , Cost Control Management , Component Costing Departments.
COSTOPTIMIZER® Professional
Is a Multi Stage Incremental Simulation from Forming Suite Product Portfolio. It’s a Tool Designers Tool to validate and establish the Tool Design Intent.
It is used for validating the tooling stages before the tool is sent for Manufacturing and thus enables Virtual Prove out.
It utilizes both LSTC’s LS-DYNA non-linear, transient dynamic, 3D explicit solver and FTI’s proprietary Coupled Hybrid Inverse (CHI) solver for fast accurate results.
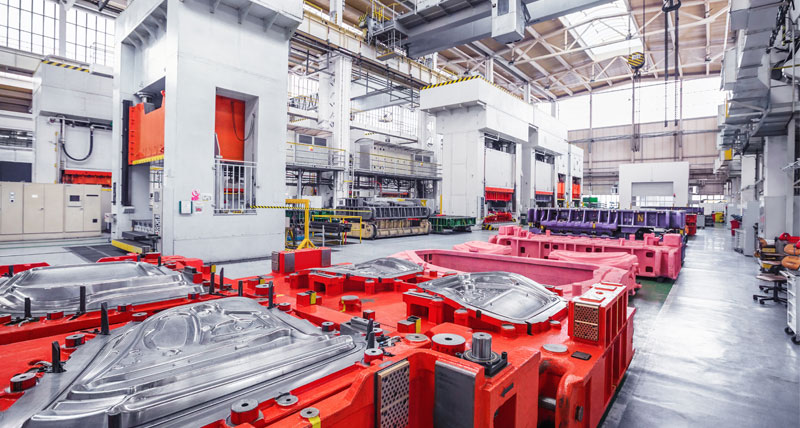
FormingSuite® SCULPTURED DIE FACE
FormingSuite® SCULPTURED DIE FACE enables cost engineers to quickly create and morph die face designs to accurately capture the true metal forming process. Drawn components require extra material (die face) to allow the required metal flow.
In just a few minutes, SCULPTURED DIE FACE quickly and easily creates hundreds of surfaces to represent the first form draw and thus provides more accurate blank shapes for drawn panels. This is essential for determining accurate material costs and scientifically estimating tooling costs.
Output of SDF can be used for Simulation purpose also.
CATSTAMP
CATSTAMP® enables users to quickly and easily evaluate part and process feasibility as well as determine blank shape and spring back. It identifies formability problems (splits/wrinkles) enabling users to implement design changes earlier in the product life cycle, saving time and money.
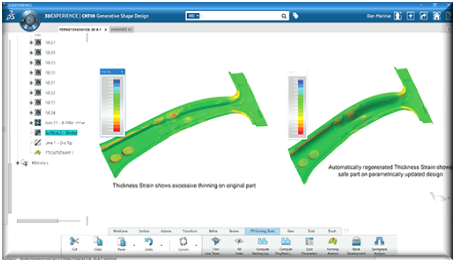
Before releasing data to tooling, engineers run CATSTAMP® to assess formability risks and optimize material usage. It considers component or tool geometry and accounts for material properties, friction, binder, addendum, blank holder force, pad pressure, draw-beads, and tailor-welded blanks.
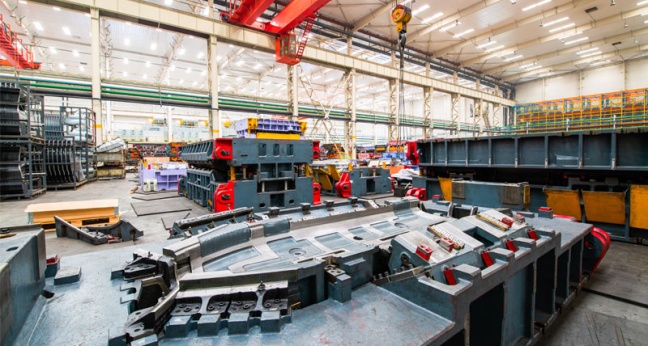
Trim Line Development
CATIA V5/V6 TRIM LINE DEVELOPMENT combines the power of FTI’s Coupled Hybrid Inverse (CHI) solver and CATIA V5/6 for development of complex hems and flanges required for Class A panels at automotive OEM and Tier 1 suppliers.
Trim Line Development is designed to quickly and accurately unfold complex geometry features such as automotive hems and flanges. The advanced capabilities make it ideally suited for tooling and process engineers, as well as method planners.